|
|
|
|
|
| Vacuum Systems >> PECVD >> PECVD Plasma Deposition System SiDep200
|
|
|
PECVD Plasma Deposition System SiDep200
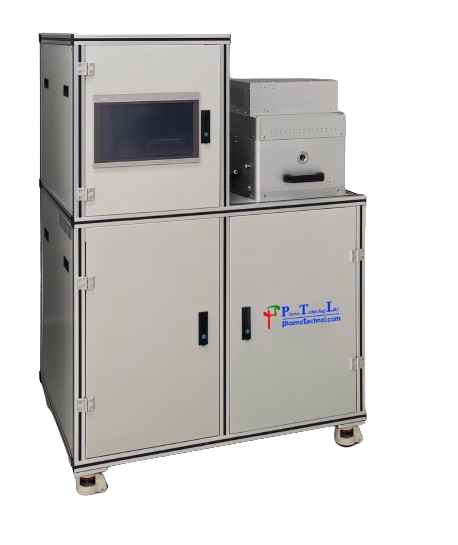
SiDep 200: PTL's foundational PECVD apparatus, integrating a parallel plate electrode configuration for homogeneous film deposition with an economically optimized direct load design. This system is engineered to accommodate standard processing on 2" to 8" wafers and sample pieces, with modular enhancements available for complex processing requirements.
Technical Highlights of the SiDep 200:
Robust System Architecture: The SiDep 200 features a durable design, ensuring operational longevity and stability under rigorous use.
System Reliability: Engineered for consistent operation, the SiDep 200 provides dependable performance, crucial for maintaining production efficacy.
Flexible Control Interface: The system boasts adaptable software and hardware, offering comprehensive control for process customization and optimization.
The SiDep 200 has been meticulously developed to facilitate a variety of processes, notably excelling in the deposition of high-fidelity silicon nitride and silicon oxide layers. The system encompasses an integrated reactor unit, precision gas box, advanced control electronics, dedicated computer, efficient backing pump, and a centralized connection box.
Configured for a broad spectrum of film depositions, the SiDep 200 is capable of depositing SiO2, SiNx, SiONx, and a-Si films within a thermal range extending to 400 degree C. It is optimally designed for the deposition of dielectric films, serving a multitude of applications including etching masks, membranes, and electrically isolating films.
Operational excellence is achieved through the PTL advanced control software, leveraging remote field bus technology for an enhanced user interface that is both technically sophisticated and intuitively accessible. The SiDep 200 represents the pinnacle of PECVD technology, delivering precision, versatility, and reliability in one comprehensive package.
Technical Specifications:
Reaction Chamber |
: |
450 x 450 x 200 (mm); Inner diameter F390;
Aluminum Alloy with anodized treatment for inside and outside surfaces;
F20mm view port with Quartz;
Open loading design; |
Electrode Structure |
: |
Parallel plates structure;
Manually adjustable electrode distance for the range of 10 - 50mm; |
Upper Electrode |
: |
Aluminum integrated shower type manifold;
F260mm, three-layer air distribution structure; |
Lower Electrode |
: |
Stainless steel (surface treated);
F266mm substrate tray with 8 inches recess and compatible for small samples; |
Substrate Heating |
: |
Automatic heating;
RT to 400oC;
F225 stainless steel armored heater;
PID control by Japan Yamatake SDC15 temperature control meter; |
Pumping System |
: |
Automatic pumping;
KYKY Turbomolecular pump: 300L/S;
Vortex dry pump: 8L/S;
Exhaust angle valve and pipes to connect TMP pump and dry pump;
CF100 pneumatic gate valve;
VAT KF40 butterfly valve for working pressure control;
Venting valve; |
Vacuum Measurement |
: |
Full-scale Inficon MPG400 vacuum gauge (5x10-7Pa~1.0x105Pa );
Inficon capacitance diaphragm gauge CDG025D 10torr (1.33x10-2~1.33x102Pa) (connected to auto pressure control valve); |
Vacuum Condition |
: |
Ultimate vacuum better than =5.0 x 10-4 Pa;
Preservation pressure better than =3.3Pa/30min; |
Gas Inlet Lines |
: |
6 mass flow controllers including by-pass line;
SiH4, N2O, NH3, CF4, N2, O2; |
Gas Inlet Valve |
: |
Japan FUJIKIN pneumatic diaphragm VCR valve; |
Process Gas Lines |
|
SUS 316L, 1/4 inches, SUS VCR fittings; |
Purge/Vent Gas Lines |
|
SUS 316L, 1/4 inches, SUS VCR fittings;
Automatic purging; |
Plasma Source |
: |
13.56MHz, 500W or 1000W, crystal oscillation, all solid-state RF generator; Double vacuum capacitors automatic matching device;
RF switch for stress control;
In-situ plasma clean; |
System Control |
: |
PLC + touch screen;
15-inch color touch screen;
English display;
3 levels management access to avoid unexpected configuration amendments, admin level to edit user, recipe and system config;
Automatic pumping, automatic heating with temperature setting, automatic purging with flow rate setting and working pressure control;
Auto process control by loading recipe;
Manual control for process by parameters setting;
Recipe management;
Data management with logging function for display, edit and save; |
Protection |
: |
Main power switch;
Emergency stop switch;
Warning buzzer; |
Interlock |
: |
Water interlock;
Vacuum interlock;
Valves interlock;
Pumps interlock;
RF power interlock; |
Power Input |
: |
3-phase 380V, 50Hz, 25A; |
Footprint |
: |
1200 mm x 1000 mm; |
Weight |
: |
~500kG; |
Closed-loop Chiller (optional) |
: |
1 set of ~1HP PID Closed-loop cooling Chiller digital temperature controller / display for the system to do the cooling for chamber, pump, etc. Configured for 220V, 50Hz input power; |
Air Compressor (optional) |
: |
1 set of air compressor to provide ~0.2-0.5MPa air pressure for the system to control valves. Configured for 220V, 50Hz input power; |
Scrubber (optional) |
: |
Heat-wet Scrubber;
2 input for toxic gases for SiH4 and other exhaust gases such as PH3, B2H6, H2, CH4, NF3, NH3, GeH4, etc
Treatment capacity of about 600SLM
Width 900mm x Depth 700mm x Height 2200mm;
Weight of about 360kG; |
|
|
Hits:2928 Input time:6/5/2024 【Print】 【Back】 |
|
 |
 |
|
|
|